Screw extruder technology innovation ushers in a new era for complex material processing
Published Time:
2025-05-27
With the market application of this technological upgrade, the processing of complex materials will become more efficient and precise, and product innovation in related industries will usher in new opportunities. This technological breakthrough not only reflects the company's leading position in the field of mechanical manufacturing, but also sets a new benchmark for technological advancement in the entire industry, leading screw extruder technology to a higher level.
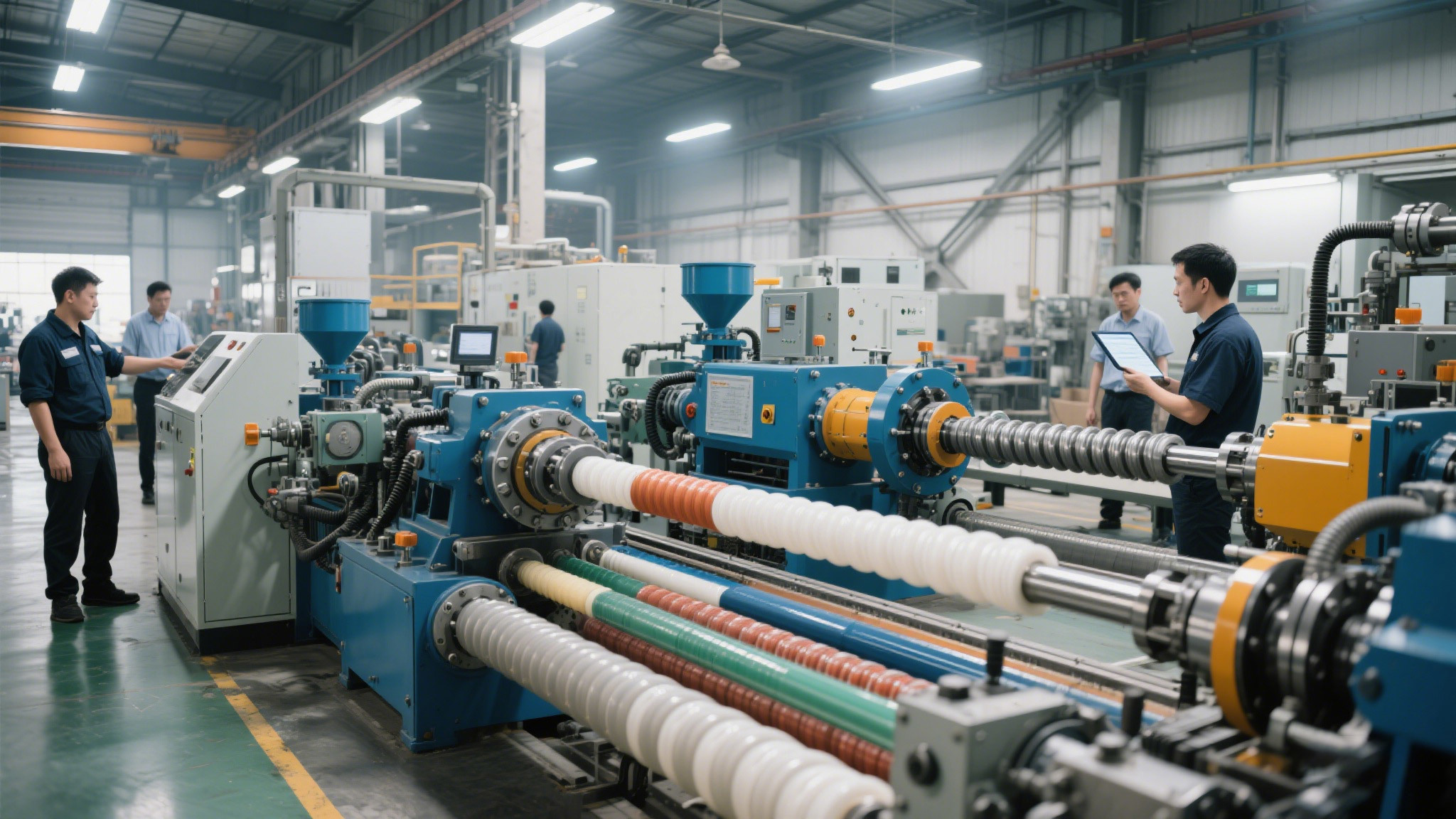
In today's rapidly advancing materials science, high-performance composites, biodegradable materials, and other complex materials are finding increasingly widespread applications in numerous fields such as automotive, aerospace, and environmental protection due to their unique performance advantages. However, the processing of these complex materials has always been a challenge in the industry, placing extremely high demands on key equipment such as screw extruders. Recently, a well-known mechanical engineering company, leveraging its deep technological accumulation and continuous innovation, has implemented a major technological upgrade to its screw extruder, successfully achieving efficient and stable co-extrusion of complex materials, injecting new vitality into the development of related industries.
The core of this technological upgrade lies in the introduction of multi-stage mixing elements. Traditional screw extruders, when processing complex materials, have limited mixing capabilities, making it difficult to achieve uniform mixing of materials with different properties at the microscopic level, resulting in unstable final product performance. The multi-stage mixing elements developed by this company cleverly design multiple mixing zones with different functions. During material transport, the materials first pass through a coarse mixing zone for initial dispersion and pre-mixing; then they enter a fine mixing zone, where a special screw structure and shear field further refine and disperse the materials; finally, in the homogenization zone, the mixed materials reach a highly uniform state. This gradual and refined mixing method effectively overcomes the compatibility differences between complex materials, allowing the materials to fully blend at the microscopic level, greatly improving the co-mixing effect.
To ensure the stability and accuracy of the entire extrusion process, the company has also equipped the screw extruder with an advanced dynamic feedback control system. This system uses multiple sensors installed inside the barrel to monitor key parameters such as material temperature, pressure, and flow rate in real time, and transmits this data to an intelligent control center. The control center uses advanced algorithms to analyze and process the data. Once an abnormality in the material mixing state is detected, such as excessive temperature fluctuations or uneven pressure, the system automatically adjusts equipment operating parameters such as screw speed and heating power to quickly restore stability to the extrusion process. This intelligent dynamic adjustment mechanism avoids the lag and inaccuracy of manual intervention, ensuring the quality stability of complex materials during the extrusion process, effectively improving product consistency and yield.
Taking the automotive industry as an example, high-performance composite materials play an important role in automotive lightweighting and improving fuel efficiency. However, these composite materials are usually composed of many different types of resins, fibers, and other materials, making them extremely difficult to process. Using the upgraded screw extruder, automotive parts manufacturers can more efficiently produce composite parts with stable quality and excellent performance, providing strong support for automotive lightweight design and performance improvement. In the environmental protection field, the application of biodegradable materials is crucial for reducing plastic pollution. This screw extruder can accurately achieve co-extrusion of biodegradable materials and other additives, producing biodegradable plastic products that meet environmental standards and have excellent performance, promoting the development of the environmental protection industry.
The technical director of the well-known mechanical engineering company stated: “We always pay attention to industry development trends and customer needs, and are committed to solving problems in the field of material processing through technological innovation. This technological upgrade of the screw extruder is the result of our team's long-term efforts. We hope that through this technological breakthrough, we can provide higher-quality material processing solutions for the automotive, aerospace, and environmental protection industries, helping related industries achieve leaps and bounds in product performance and innovative development, and also contribute to the transformation and upgrading of the entire manufacturing industry.”
Next
Related News