New granulation system, reshaping the landscape of the plastics granulation industry
Published Time:
2025-05-27
A machinery company recently launched a new plastic granulation system. This system, with its innovative screw structure and efficient heating and cooling technology, has significantly improved the efficiency of plastic granulation. The new system's screw design optimizes material conveying and plasticizing, increasing granulation speed by 40% compared to traditional equipment. At the same time, the precise heating and cooling system can quickly and stably adjust the temperature, ensuring that the plastic raw materials are processed under optimal conditions, guaranteeing product quality. Furthermore, this granulation system has made a major breakthrough in automation, achieving fully automated operation throughout the entire process, reducing manual intervention, lowering labor intensity, and improving production stability and consistency. The advent of this new granulation system provides plastic processing enterprises with a more efficient and intelligent production solution, and is expected to trigger a new round of technological innovation in the field of plastic granulation.
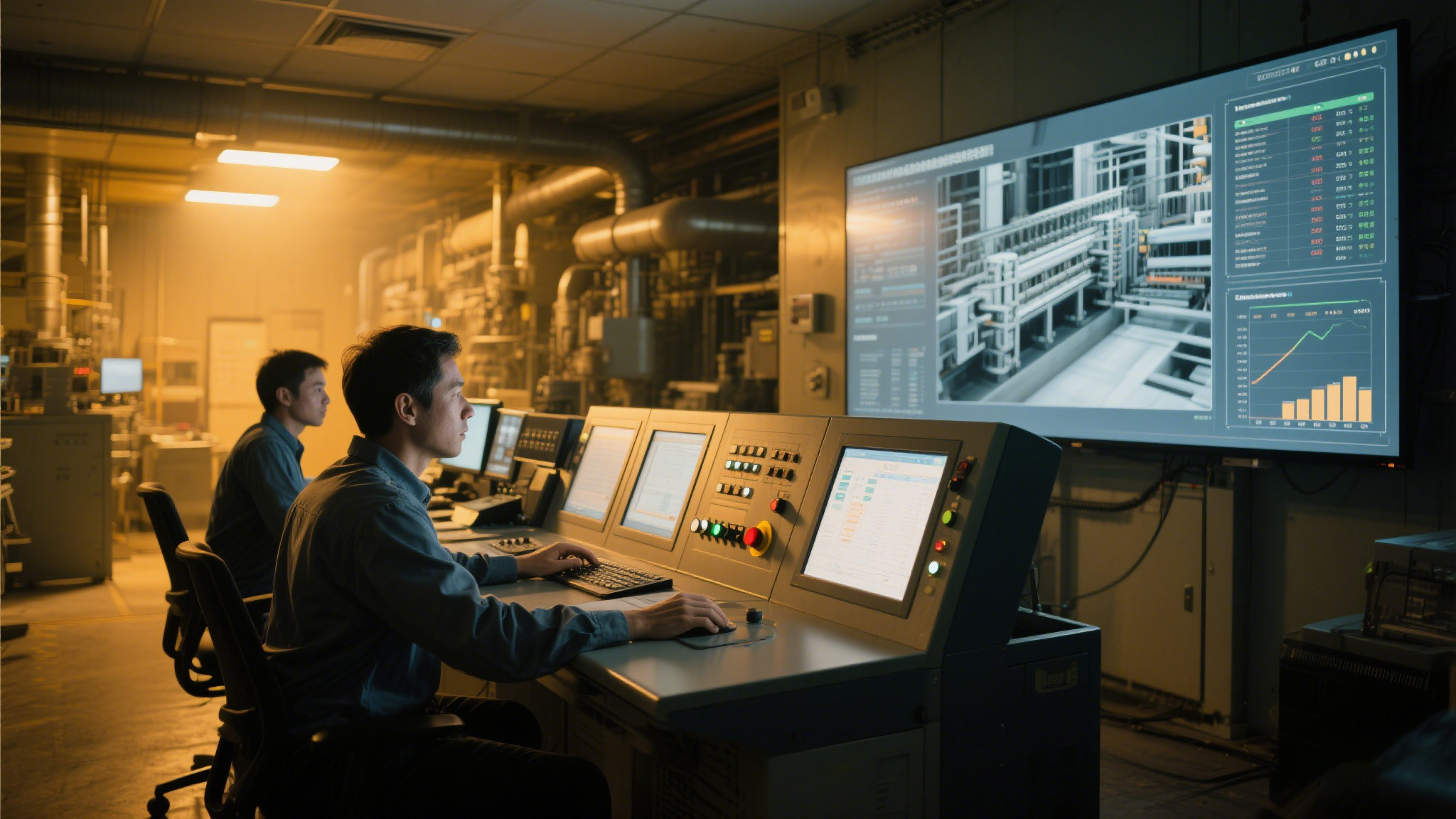
In the plastics processing industry, granulation is a fundamental and crucial process whose efficiency and quality directly impact a company's production costs and product competitiveness. With the continued growth in market demand for plastic products, improving granulation efficiency and optimizing product quality have become pressing issues for many companies. The Machinery Company has long focused on the research and development and manufacturing of plastic processing equipment, deeply understanding industry pain points. After years of technological breakthroughs and innovative practices, it has successfully launched a new, high-performance plastic granulation system, injecting new vitality into industry development.
One of the core advantages of the new granulation system lies in its unique screw structure design. Traditional screws, when processing plastic raw materials, often suffer from problems such as poor material transport and uneven plasticization, limiting granulation speed and product quality. The Machinery Company's new system uses a novel multi-head thread and variable-pitch screw design. The multi-head thread increases the contact area between the material and the screw, allowing the material to advance more quickly during screw rotation; the variable-pitch design flexibly adjusts the feed speed and shear force according to the state of the material at different positions in the barrel, achieving efficient plasticization of the material. Actual production tests show that the granulation system using this new screw structure has significantly increased granulation speed by 40%, meaning that companies can produce more plastic particles in the same amount of time, greatly improving production capacity.
Precise temperature control is crucial for plastic granulation. Excessive temperature can lead to the decomposition and discoloration of plastic raw materials, affecting product performance; too low a temperature will result in incomplete plasticization of the material, causing particle quality defects. The new granulation system is equipped with advanced heating and cooling technology, using high-precision sensors to monitor the temperature of each area within the barrel in real time and automatically adjusting the operating status of the heating elements and cooling devices through an intelligent control system. This system can quickly adjust the temperature to the set value in a short time and control temperature fluctuations within a very small range, ensuring that the plastic raw materials are always granulated under optimal temperature conditions. This technological innovation not only improves the product yield but also ensures that the produced plastic particles have better performance stability and consistency, meeting the market demand for high-quality plastic products.
In terms of automation, the Machinery Company's new granulation system has achieved a qualitative leap. From the feeding, conveying, plasticizing, and granulation of plastic raw materials to the collection of finished products, the entire production process can be operated through an automated control system. Operators only need to set various parameters in the control system, and the equipment will automatically run, completing a series of complex production tasks. The automated system also has fault diagnosis and alarm functions. Once the equipment encounters an abnormal situation, it can promptly issue an alarm and indicate the cause of the fault, allowing maintenance personnel to quickly handle it, effectively reducing equipment downtime. This highly automated design not only reduces manual labor intensity and minimizes the interference of human factors on the production process but also improves production stability and reliability, providing strong support for companies to achieve large-scale, standardized production.
[X] The technical director of the Machinery Company stated: “We always focus on customer needs and are committed to providing the plastics processing industry with more advanced and efficient equipment. This new granulation system embodies the years of R&D efforts of our team, and from design concept to technical implementation, it has undergone repeated verification and optimization. We believe that it will bring significant economic and social benefits to a wide range of plastic processing companies and promote the development of the entire plastic granulation industry to a higher level.”
With the gradual promotion and application of this new granulation system in the market, plastic processing companies will usher in a more efficient and intelligent production era. Companies can use this advanced equipment to enhance their market competitiveness, seize opportunities in fierce market competition, and achieve sustainable development. At the same time, the successful launch of this system will also encourage more machinery manufacturing companies to increase investment in technological innovation and jointly promote technological progress and industrial upgrading in the plastics processing industry.
Related News